For Derek Uhlman, a sculptor of 40-plus years’ experience, computer-aided design or “CAD” technology has dramatically changed the artist’s ability to visualize ideas and make them a reality.
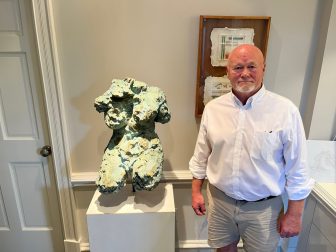
Sculptor Derek Uhlman with a bust at his Pine Street gallery. Credit: Michael Dinan
A Michigan native who trained as an apprentice under Reuben Nakian and earned his first major commission in 1982 from the General Food Corporation (a 37,000-pound marble sculpture), Uhlman also acknowledges that 3D design and fabrication also have “accelerated the design and visualization process, so an idea can form much quicker.”
“There are aesthetic struggles in the fine arts,” Uhlman told NewCanaanite.com on Monday afternoon. “One of the things about 3D printed objects is that they are geometrically perfect because the CAD system is very, very precise. Thousandths of an inch or thousandths of a millimeter if you want it to be. One of the beauties of a handmade artwork is its handmade characteristics. So one of the things I aesthetically struggle with as an artist is how to introduce some naturally occurring characteristics to a 3d printed artwork. I’ve been developing ideas for randomness. How to introduce randomness, and it turns out there are ways to do that and I feel I’m having success at it.”
For years, Uhlman has worked out of his home studio in Norwalk—a noisy place where stonedust is hostile to computers—as well as another metal fabrication studio in New Rochelle, N.Y.

The 3D MakerLab machines at Derek Uhlman’s studio and gallery on Pine Street. Credit: Michael Dinan
This summer, he opened a new gallery and studio in downtown New Canaan that honors his traditional fine arts roots while embracing rapidly developing technology and the future of sculpture. At Refine Design 3D LLC, a serene three-room space located at 70 Pine St., Uhlman displays pieces he creates using both traditional sculpting methods—for example, a female torso hammered out of a lead sheet—and advanced fabrication.
While collectors, curators and dealers can purchase works exhibited at the gallery, the space also serves as a kind of consultancy for Uhlman, who is expert enough in 3D advanced manufacturing to advise and assist on projects from fellow fine artists and in other professions, such as furniture design and architecture.
When Uhlman started doing 3D design work, he did it to develop his own designs.
“And it has since expanded into other things,” he said.

Sculptor Derek Uhlman with shelves of his work his Pine Street gallery. Credit: Michael Dinan
For example, one of the shelved designs in his studio is a red plastic 3D model of a cupola that he created for a client. The full-scale version of that same cupola now is several feet tall and sits atop a building of his design with a “nice copper roof on it,” he said.
He also used 3D scanning and printing recently to create a custom-fitted plastic wrist brace for his wife as part of her orthopedic recovery, replacing a fabric brace that she couldn’t wear while taking a shower because hot water would distort it.
“In some cases, it’s practical applications that are a product of some kind,” Uhlman said.
And in other cases, it’s fine art just like the bronze torso inside the door at Refine Design. Part of the gallery on Pine Street features five black-and-white 3D design pieces that have been selected for an upcoming exhibition—one of which also was cast in bronze and is displayed on a table in the main gallery room.
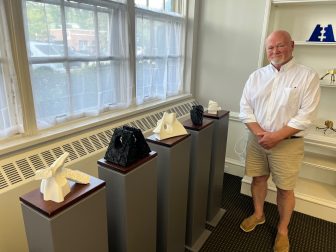
Sculptor Derek Uhlman with 3D rendered work at his Pine Street gallery. Credit: Michael Dinan
In another instance, a sculptor from Brooklyn created a model out of “taped-together cardboard,” Uhlman said, that he then 3D-scanned in order to manipulate using advanced computer software. The sculptor ultimately wanted it made out of stainless steel.
“It stands about three feet tall,” Uhlman said. “It had 96 different surfaces. All these different surfaces, none of which were identical. And so, it involved taking that form, breaking it into its individual parts and composing them in a fashion that they could be sent out to a company that does laser fabrication, laser cutting.”
For fine artists as well as artisans, part of Uhlman’s service is not only using 3D technology to help them realize the projects that they envision, but also connecting them with vendors who have rare and specialized tools.
Last week, for example, a high-end furniture designer came forward with an unusual project: an irregularly shaped, 1.75-inch glass top to a table.
“He’s going to use a company that has water jet cutting,” Uhlman said. “It uses a water jet that’s something like two hundred thousand [PSI].”
That’s a specialized process that his client didn’t know about, and the vendor that does the glass-cutting needed a 3D file in a format that the furniture designer didn’t have and didn’t know how to obtain.
“There’s things you couldn’t do before at all, and now, because of these technologies, people can do them,” Uhlman said. “So that’s where I come with the phrase ‘humanizing’ it and ‘providing an inroad.’ So here we have a guy who’s a furniture designer. He now knows it’s possible. He doesn’t know how to go about it, but he knows it’s possible.”
Uhlman has worked in sculpture pretty much from the time he could work at all. His family moved to Stamford in 1961 and Uhlman began creating jewelry in the early-1970s, when he was still a teenager. He made his first sculptures in 1978 and studied bronze casting and drawing at the State University of New York in Purchase, N.Y. and clay modeling, molding and casting and stone carving at the Silvermine Guild of Artists, present-day Silvermine Arts Center in New Canaan (he served on its Board of Directors in the 1980s). He started working as an assistant with the sculptor Ivan Biro in 1980 and with Nakian in 1981.
His sculptures have been acquired by Rockefeller Center, General Electric Corp., Kraft General Foods and Daiwa Corporation for display at its headquarters in Tokyo. Uhlman’s works have been exhibited at institutions including the National Academy of Design in New York City, Smithsonian Institution in Washington, D.C. and the Kouros Sculpture Center in Manhattan.
Even with his formidable formal training and success in sculpture, Uhlman said he “jumped at the idea” of using 3D CAD work when it became possible to do on a PC (instead of a server-mounted computer, as it was 25 years ago).
“I thought it was very intriguing, to develop my ideas to learn the technology,” he recalled. “I then was able to work with an industrial designer friend I know who used the kind of computers that, for example, ‘The Terminator’ special effects were done on. And I actually bought a machine from him, which was about the size of a dishwasher. A serious machine. And so he gave me some instruction and then I just continued doing it. But I’ve been learning it myself for years.”
And it’s helped not just Uhlman but other artists as well as artisans.
Speaking about the furniture designer, Uhlman said, “He was thrilled to find out about me. You know, people are asking, ‘do you know anybody who knows how to do this stuff?’ And that’s why I’m doing this. Because people are looking for people.”
Refine Design 3D LLC at 70 Pine St. is open by appointment. Sculptor/owner Derek Uhlman can be reached at derekuhlman@uhlman.com.